Screw air compressors are essential foundational products in modern industrial automation. As the core power source of pneumatic systems, they convert mechanical energy—usually from an electric motor—into compressed air pressure energy. This compressed air powers various industrial processes, making the choice of the right screw air compressor critical.
This guide presents 10 key principles for selecting the ideal screw air compressor for your needs, helping you optimize efficiency, reliability, and energy savings.
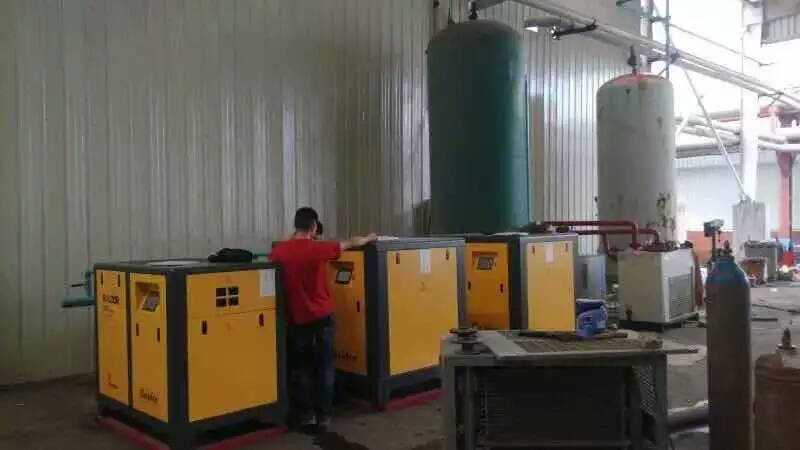
1. Understand Your Compressed Air Application
The first step is to clearly identify the purpose of the compressed air in your operations. Different applications demand varying pressure levels, airflow volumes, and air quality standards.
2. Determine the Minimum Operating Pressure
Specify the lowest pressure at which your system must operate reliably. This ensures your compressor isn’t oversized or underperforming.
3. Evaluate Peak and Off-Peak Airflow Requirements
When the pressure difference between peak and off-peak usage exceeds 3 bar, it’s advisable to consider a dual-pressure system. This involves selecting different compressor models based on demand:
- Base load: Centrifugal compressors (for units > 75 CMM) or rotary screw compressors (for units < 60 CMM).
- Variable load: High-pressure compressors combined with large air receivers to handle fluctuating demand.
Explore Baldor’s centrifugal and screw compressors.
4. Match Air Quality Needs with Dryers and Filters
Select appropriate types and grades of dryers and precision filters based on your process’s air quality requirements. Over-specification wastes energy, while under-specification can affect product quality.
5. Utilize Advanced Control Technologies
Modern compressors incorporate technologies like:
- Multi-unit linkage controls
- Variable speed drives (VSD)
- Remote monitoring systems
These technologies can reduce electric costs by 25–40%, decrease backup capacity needs by 15–30%, and maintain stable air pressure within ±0.1 bar.
See how Baldor’s variable frequency drives enhance energy efficiency.
6. Focus on Actual Operating Efficiency
Don’t rely solely on catalog horsepower or nominal airflow. Instead, assess actual performance curves and specific power consumption (air volume per kilowatt) for true efficiency insights.
7. Plan for Installation Space and Environment
Consider compressor room size, ventilation, noise isolation, heat recovery, and wastewater treatment when planning installation. Centralized systems usually offer lower installation, maintenance, and control costs compared to distributed setups.
8. Choose Between Air Cooling and Water Cooling
- Air-cooled compressors: No need for cooling towers but require good ventilation.
- Water-cooled compressors: Offer stable operating temperatures unaffected by ambient conditions, promoting longer lifespan but may require freeze protection.
9. Ensure Stable and Adequate Power Supply
Plan for reliable voltage supply and minimal voltage drops. Centrifugal compressors often require high voltage and fixed installations, which may impose restrictions on mobility and startup impact on the power grid.
10. Provide Adequate Maintenance Space and Facilities
Design your compressor room with sufficient space for routine maintenance, including:
- Crane or hoist access
- Clear passageways for equipment movement
- Proper training for technical personnel on compressor maintenance
Conclusion
Choosing the right screw air compressor involves carefully balancing operational requirements, energy efficiency, maintenance considerations, and technological advances. With Baldor’s extensive range of high-performance compressors and expert support, you can optimize your compressed air system to meet your industrial needs efficiently.
For personalized assistance, contact our engineering team today.