Screw air compressors are essential in modern manufacturing, but they are also major energy consumers. With rising electricity prices and growing demand for sustainability, improving the efficiency of your air compressor system is more important than ever.
Upgrading to a Permanent Magnet Variable Speed Drive (PM VSD) screw air compressor is a smart first step. But to fully unlock the energy-saving potential, it’s crucial to implement best practices throughout your system. Below are eight proven strategies to help businesses reduce power consumption and cut operating costs.
🔗 Learn more about Baldor’s energy-efficient PM VSD air compressors and how they help manufacturers reduce electricity bills.
1. 🔧 Eliminate System Leaks
Even a 1mm² leak at 7 bar can result in an air loss of around 1.5 liters per second. Over time, this adds up to significant energy waste. Regularly inspect and repair leaks around piping joints, valves, and end-use tools to reduce losses and save power.
2. 📉 Reduce Pressure Drop
Monitor and control pressure drop throughout your compressed air network.
- Total drop from compressor to end use: < 1 bar
- Ideal: < 0.7 bar (or 10% of working pressure)
- Dryer + filtration section: ~0.2 bar
Using ring networks and distributed pressure gauges can help balance air supply across different points.
3. 🎚️ Optimize Discharge Pressure
Avoid setting your compressor pressure higher than necessary. For every 1 bar reduction in discharge pressure, you can achieve 7–10% energy savings. Analyze actual demand and tune the pressure settings to match.
4. 🚫 Avoid Misuse of Compressed Air
Studies show that only 10% of compressor energy goes to productive use—the rest turns into heat. Audit air-powered tools and processes; replace with electric tools where practical, and avoid using compressed air for cleaning or cooling non-essential equipment.
5. 🔗 Use Intelligent Centralized Control
If your facility runs multiple air compressors, centralized coordination is key.
- For 1–2 units: A single PM VSD compressor can manage pressure.
- For 3+ units: Use a centralized control system to balance operation, reduce idle time, and avoid pressure spikes from uncoordinated loading.
6. 🧼 Maintain and Clean Equipment Regularly
Efficient cooling is critical to performance. Ensure your heat exchangers (air-cooled or water-cooled) remain free of dust, scale, and clogs. Also, keep lubricant clean to prevent energy-robbing internal friction.
7. ♻️ Recover and Reuse Waste Heat
Up to 90% of input energy in a screw compressor turns into heat. With proper heat recovery systems, this waste heat can be captured from the oil circuit and reused to produce hot water for process heating or facility washrooms, significantly reducing energy bills.
8. 💨 Upgrade the Dryer System
Traditional dryers consume additional energy. By retrofitting or replacing them with new-generation dryers that use compressor waste heat for air drying, you can reduce energy use by over 80%.
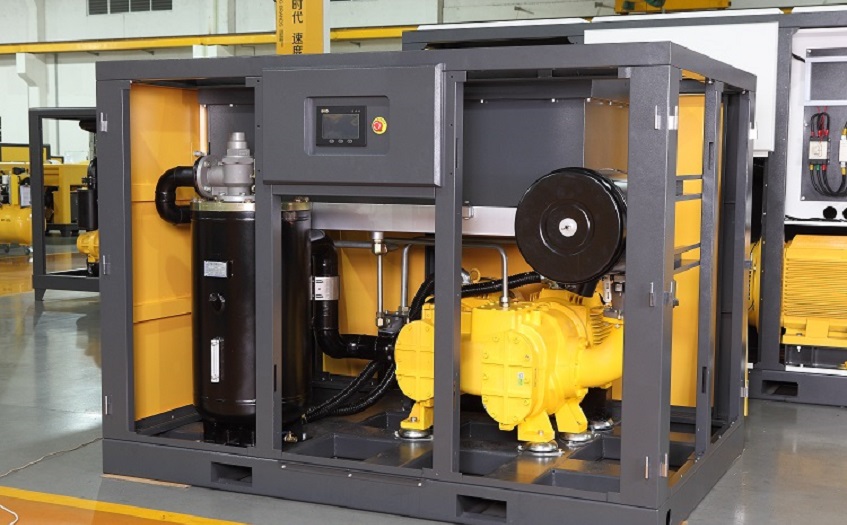
✅ Conclusion: Optimize from the Inside Out
Implementing these eight energy-saving paths—from leak prevention to waste heat reuse—can significantly reduce your compressor system’s power usage. For facilities already using PM VSD screw air compressors, these upgrades and practices offer ongoing ROI and sustainability benefits.
Want to upgrade or optimize your air system?
🔗 Explore our full range of Baldor energy-efficient air compressor solutions.