When opening a new factory or expanding production capacity, choosing the right air compressor is a crucial decision that goes beyond just the initial purchase cost. Key considerations include how to reduce ongoing electricity expenses, extend the lifespan of your compressor, maintain consistent air pressure, and minimize environmental noise and pollution. These are all important factors that need to be addressed when setting up an air compressor system.
How to correctly select an air compressor in the initial stage of factory establishment?
1.Identify Compressed Air Requirements:
The first step is to understand your factory’s entire manufacturing process and determine where compressed air is needed. Identify key points where air is consumed and estimate the required volume.
2.Calculate Key Compressor Parameters:
Once you know the air consumption points, you can calculate the overall air demand. If you’re not familiar with specific technical data, you can refer to similar industry setups or consult Baldor’s air compressor experts for guidance. Generally, you’ll need to calculate important parameters like power, airflow, and pressure. A good rule of thumb is to choose a compressor with airflow capacity that is approximately 20% higher than the maximum air demand to account for pressure losses and potential future expansion needs.
3.Consider After-Treatment Equipment:
Depending on your air quality requirements, you will need the appropriate level of after-treatment equipment, such as dryers and precision filters. Overly high-quality equipment wastes energy, while insufficient air quality could impact production quality. It’s important to balance energy efficiency with production needs.
4.Installation Considerations:
The installation space, ventilation, noise insulation, and heat recovery systems all play a role in the overall energy efficiency of the system. A centralized system is often more cost-effective in terms of installation, maintenance, and control compared to a distributed one, reducing the need for additional equipment.
5.Choose a Reliable Brand:
It’s always advisable to choose a trusted brand like Baldor, known for its superior technology, product quality, and robust after-sales service.
Case Study: Choosing an Air Compressor for a New Factory
About Xiede New Materials Technology Co., Ltd.:
Located in Jiangmen, Guangdong Province, Xiede New Materials specializes in the research and production of innovative environmentally friendly materials, including foam and plastic products. The company opened a brand-new automated production line in March 2020 and required a reliable, energy-efficient air compressor system to support its production needs.
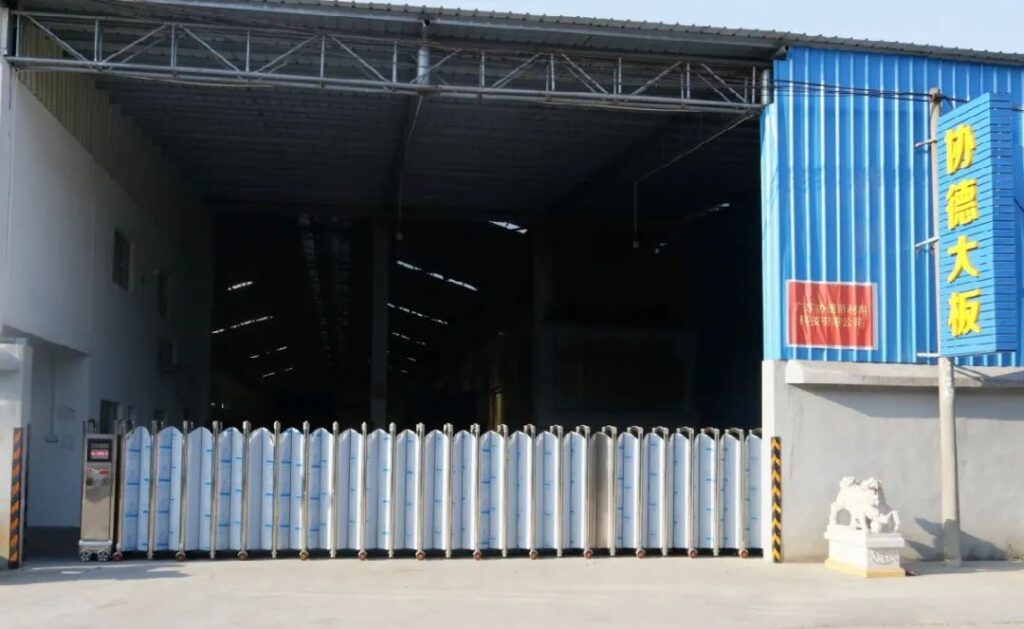

The Baldor Solution:
To meet the demands of its new factory, Xiede partnered with Baldor and selected the BD-100PM-II intelligent permanent magnet variable frequency compressor. Baldor provided comprehensive services, including air demand calculations, equipment s election, post-treatment configuration, installation, and operator training, ensuring a seamless integration of the air compressor system into Xiede’s production process.
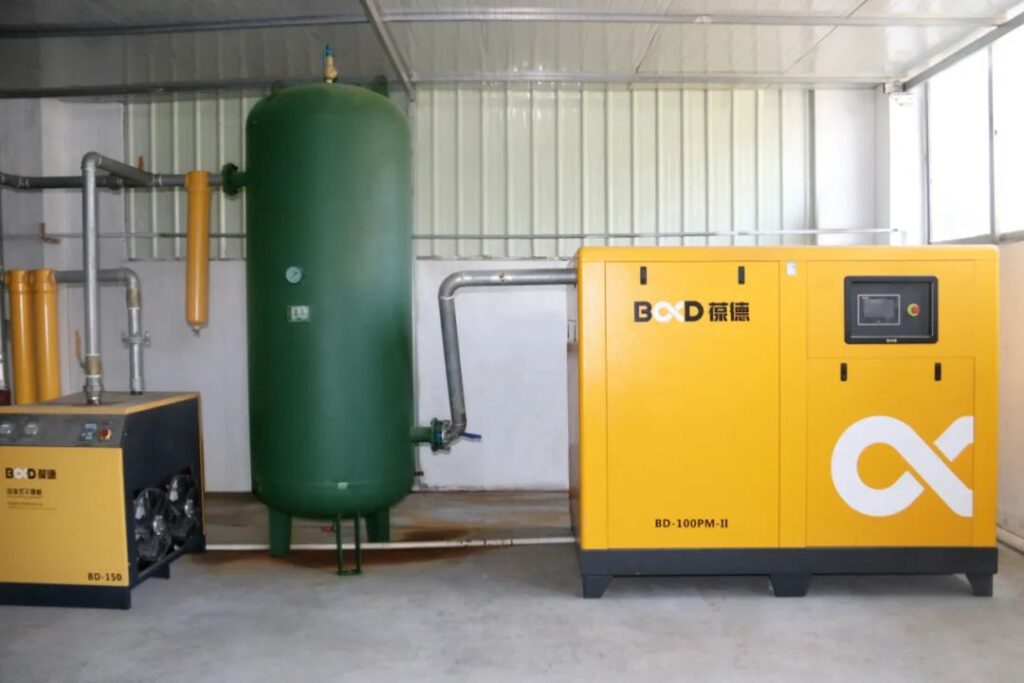
Energy Savings Results:
After using Baldor’s intelligent permanent magnet variable frequency compressors for over six months, Xiede’s electricity costs were significantly reduced. The company’s monthly electricity bill for producing 150 tons of foam products dropped from 200,000 RMB to around 150,000 RMB, saving approximately 50,000 to 60,000 RMB per month. Over just a few months, Xiede had saved enough to cover the cost of one compressor!
Feedback from Xiede’s Management:
Mr. Huang, the General Manager of Xiede New Materials, shared his thoughts on using Baldor compressors:
“Baldor and Xiede are well matched – both companies value product quality. Baldor’s intelligent permanent magnet variable frequency technology is industry-leading, with automatic adjustment of discharge pressure, ensuring stable and reliable operation. With the integration of Baldor’s smart IoT technology, we can monitor the machine’s status via smartphone and receive timely maintenance reminders, providing peace of mind and convenience. We truly appreciate Baldor’s commitment to quality and service.”
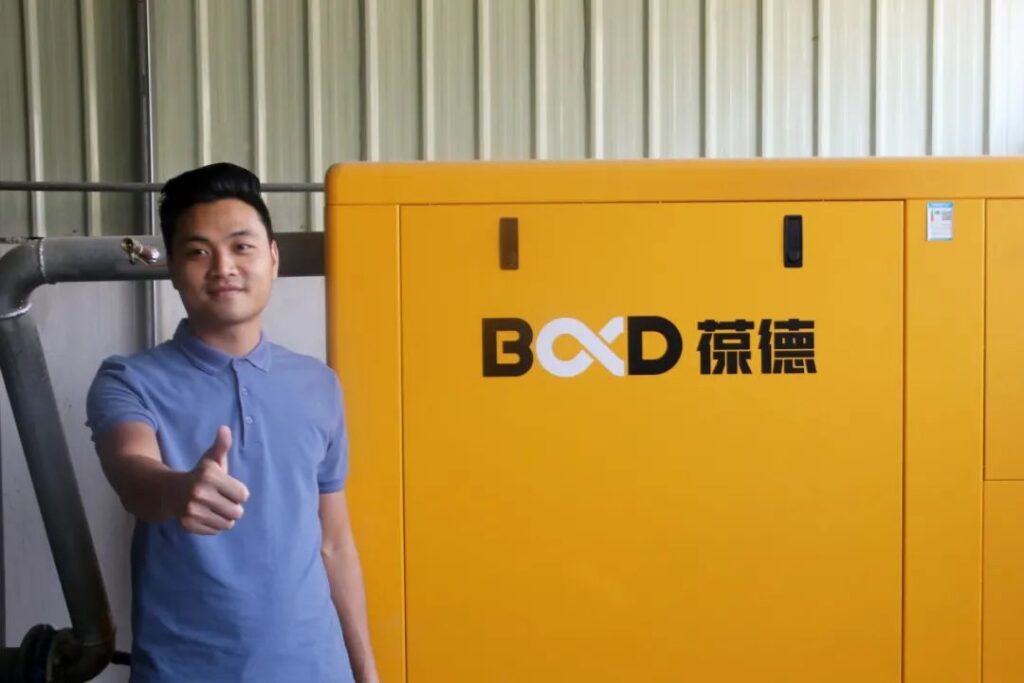
Conclusion:
Choosing the right air compressor for your new factory is a decision that impacts both operational efficiency and long-term cost savings. By partnering with Baldor, Xiede New Materials successfully reduced its energy consumption and operational costs while ensuring a stable air supply for production. Baldor continues to provide energy-efficient, high-performance solutions that support businesses in improving their production processes and reducing costs.
Learn More About Baldor’s Energy-Saving Solutions:
To discover how Baldor can help your business achieve energy savings and boost operational efficiency, visit Baldor Air Solutions.