To ensure reliable operation and extend the service life of your screw air compressor, it’s essential to implement a structured maintenance plan. This includes designated operators, regular inspections, and periodic servicing. Keeping the equipment clean, oil-free, and free from dust buildup is vital to long-term performance.
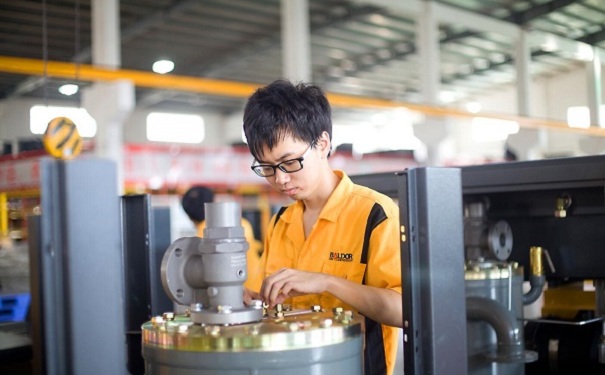
1. Routine Maintenance of Main Components
Follow the recommended schedule for component servicing. During maintenance or replacement, always ensure the following:
- All internal pressure is fully released.
- The compressor is disconnected from all power sources.
- Proper safety tags are in place to prevent accidental startup.
Important Notes:
- Lubricant replacement depends on environmental factors such as humidity, dust levels, and the presence of corrosive gases.
- For new compressors, replace the lubricant after the first scheduled run-in period, then follow normal replacement intervals.
- When servicing air filters or intake valves, avoid letting debris fall into the compressor chamber. Always seal the inlet during work and manually rotate the rotor post-service to check for obstructions before restarting.
- Inspect belt tension every 2,000 hours of operation. Adjust as needed and avoid oil contamination on belts.
- Replace the oil filter with every oil change.
- Always use genuine parts to prevent equipment failure and ensure warranty coverage.
🔗 Learn more about air compressor filter systems and their maintenance.
2. Cleaning the Cooler
After a period of operation, the cooler needs to be cleaned to maintain efficient heat dissipation:
- Open the cooler blow-off port and use compressed air to remove surface dust.
- If dust buildup is severe, remove the cooler, drain the oil, seal all ports, and then clean with air or water. Ensure it’s completely dry before reinstalling.
⚠ Do not use metal brushes or sharp tools to scrape the cooler surface, as this may cause permanent damage.
3. Draining Condensate Water
Water vapor in compressed air can condense inside the oil-air separator tank, especially in humid weather or when temperatures fall below the dew point. This can lead to:
- Oil emulsification
- Poor lubrication
- Reduced oil-gas separation
- Increased internal pressure
- Corrosion of internal components
🕒 Suggested timing: Drain water before the first start-up of the day when the system is fully depressurized and cooled.
Steps to Drain Condensate:
- Remove the plug in front of the separator tank ball valve.
- Slowly open the ball valve until oil flows out.
- Close the valve and reinsert the plug.
4. Safety Valve Guidelines
Each unit is equipped with a factory-calibrated safety valve. Users should not adjust it independently. If adjustment is necessary, it must be done under the supervision of local safety authorities or Baldor-certified technicians.
❗ Unauthorized modifications may result in serious safety risks and void product warranties.
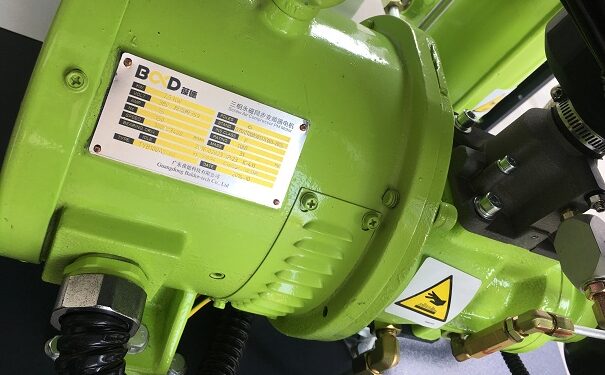
5. Regular Maintenance Schedule
Below is a general checklist for routine upkeep:
Weekly Checks
- Listen for abnormal noises or leaks.
- Check all gauge readings.
- Verify correct temperature display.
Monthly Checks
- Inspect the unit for rust or loose parts.
- Remove rust and apply anti-corrosion measures.
- Drain condensate water.
Quarterly Checks
- Clean the cooler exterior and fan blades.
- Lubricate motor bearings.
- Inspect hoses for wear or cracks.
- Clean electrical components and the control box.
Ensure you’re using our genuine spare parts to maintain system reliability.
6. Replenishing Lubrication Oil
During operation, oil levels should be maintained between the minimum and maximum marks on the sight glass.
⚠ Too much oil can affect separation efficiency. Too little oil can cause poor lubrication and overheating.
How to Add Oil:
- Shut down the compressor and ensure the system is fully depressurized.
- Disconnect the main power supply.
- Open the oil fill cap on the separator tank and add the appropriate cooling lubricant.
Conclusion
A well-maintained screw air compressor ensures stable performance, improved energy efficiency, and extended lifespan. By following the recommended maintenance schedule and using genuine Baldor components, you can avoid unexpected breakdowns and costly repairs.
Looking for professional support? Contact our service team or explore our complete maintenance solutions tailored for your industrial setup.