Screw air compressors play a crucial role in many industrial applications. Ensuring their optimal operation and longevity requires careful attention to detail in both daily use and maintenance. This article outlines the key operational procedures, maintenance checks, and safety considerations for screw air compressors.
Pre-Start Checklist for Screw Air Compressors
Before starting your screw air compressor, perform these essential checks:
- Power Supply: Ensure the power supply is connected and the indicator light is on.
- Oil and Water Drain: Open the oil-gas tank’s drain valve to release any condensate, then close it securely.
- Oil Level Check: Confirm that the oil level is above the minimum line.
- Cooling Water Flow: Check that the cooling water valves are open and the water supply is normal.
- Compressor Outlet Valve: Ensure the outlet valve is open.
- Water Separator Check: Empty the water separator cup as needed.
- Leak Detection: Inspect all connections for potential air, oil, or water leaks.
Step-by-Step Startup Procedure
Once the pre-start checklist is complete, follow these steps to safely start the screw air compressor:
- Press the “Start” button. The unit should begin running, and the “Running” indicator light will illuminate.
- Within approximately 2 seconds, the unit will automatically load, opening the intake valve. Check that the lubricating oil pressure gauge and exhaust pressure rise.
- After the compressor has loaded, verify the oil level is within the normal range.
- Inspect for any leaks or unusual vibrations. If any issues are found, shut down immediately.
- Engage the compressor’s linked control system.
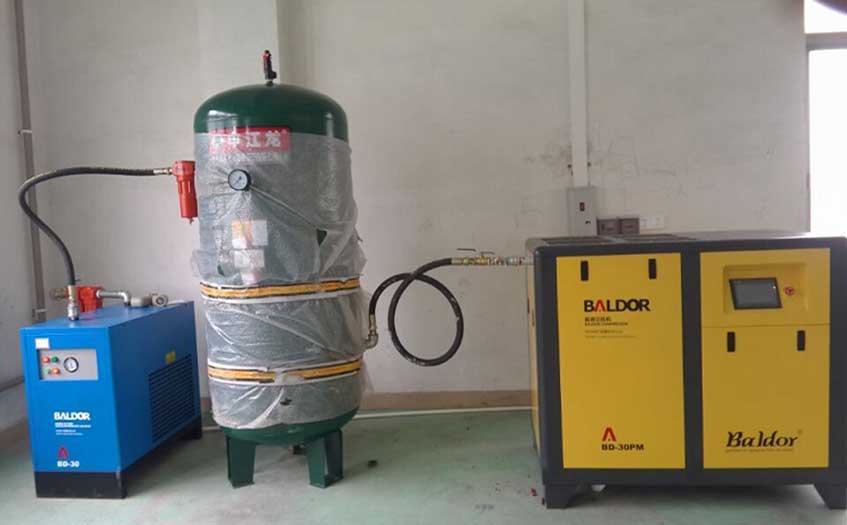
Regular Checks During Operation
To maintain optimal performance during operation, perform the following checks at regular intervals:
- Oil Level: If the oil level is too low, top up the lubricant. Ensure the compressor is shut down, and pressure is released before adding oil.
- Hoses and Connections: Regularly inspect hoses for integrity and ensure no leaks are present.
- Electrical Connections: Ensure all electrical connections are secure.
- Water Separator: Confirm the automatic discharge of condensate is functioning properly.
- Exhaust Temperature: Keep the exhaust temperature within the recommended range of 75-95°C.
- Monitoring Parameters: Periodically check voltage, current, exhaust pressure, exhaust temperature, and oil levels.
- Pressure Switch Operation: Ensure that the pressure switch is working correctly, with the compressor unloading at the upper pressure limit and loading at the lower limit.
- Soundproof Cover: Always close the soundproof cover after checking.
Key Operating Considerations
- Unusual Sounds or Vibrations: If the compressor emits unusual noises or vibrations, stop the unit immediately.
- Pressure in the Piping: Do not loosen any piping bolts or open unnecessary valves while the compressor is running.
- Oil and Temperature Issues: If the oil level decreases significantly, and the oil temperature increases, shut down the machine. Wait for the pressure to drop, then check the oil level and top it up if necessary.
- Automatic Drain Function: Regularly verify that the automatic drain is working properly to prevent moisture buildup in the system.
- Weekly Maintenance: Every week, ensure the oil-gas tank is drained and that the unit is run for at least 2 hours to maintain proper operation.
- Pressure Switch and Control System: Regularly inspect the pressure switch and control systems to avoid excessive energy consumption. Improper operation may lead to frequent starts and stops, which could damage the motor.
- Safe Operation Zones: Avoid operating the compressor in areas with flammable or toxic gases. Never block the compressor’s intake port.
- Pressure Limits: Never operate the compressor above the rated pressure. Similarly, avoid running it below the rated pressure when possible.
- Soundproof Cabinet: Keep the soundproof cabinet doors closed while the compressor is running.
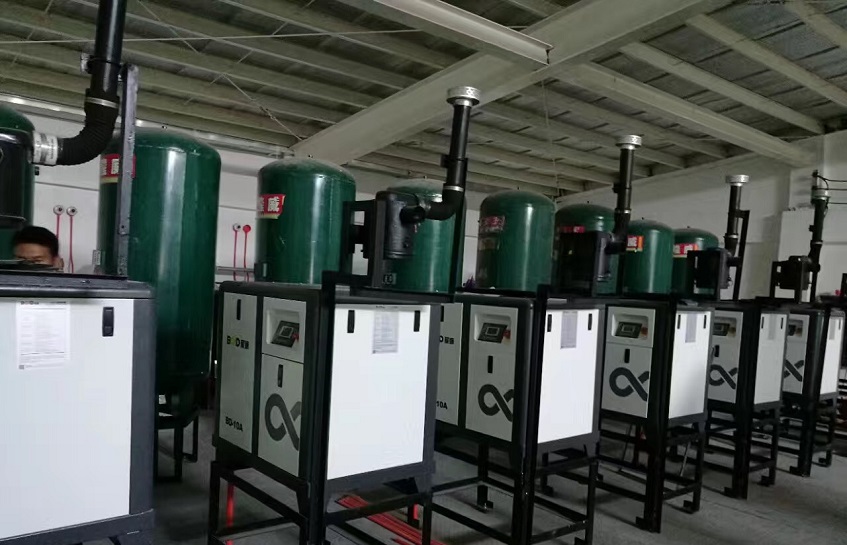
Proper Shutdown Procedure
To safely shut down your screw air compressor, follow these steps:
- Switch the compressor control to single control mode.
- Press the “Unload” button and allow the machine to run for an additional 20-30 seconds.
- Press the “Stop” button. The “Running” indicator should turn off, and the motor will stop.
- Open the exhaust valve to release any remaining condensate.
- Drain the cooling water from the cooler.
- Close the outlet valve.
Emergency Shutdown Scenarios
In the event of a critical issue, press the emergency stop button immediately. Emergency shutdown should be executed if any of the following occur:
- Fire in the motor or electrical components.
- Mechanical damage or abnormal noise, especially from components like the cylinder body, cylinder head, or rotor.
- Vibration, temperature, or current readings exceed the specified limits.
- Cooling water supply is interrupted.
Long-Term Shutdown Procedures
For periods when the compressor will be shut down for more than two weeks, follow these procedures:
- Drain the condensate from the oil cooler and aftercooler.
- Resolve any outstanding faults to ensure the unit is ready for future use.
- If the shutdown exceeds two months, in addition to the previous steps:
- Seal all open ports to prevent moisture from entering.
- Wrap safety valves and control panels with oil paper to prevent rust.
- Change the lubricating oil and run the compressor for 30 minutes before shutting it down and draining the condensate from the oil-gas tank and cooler.
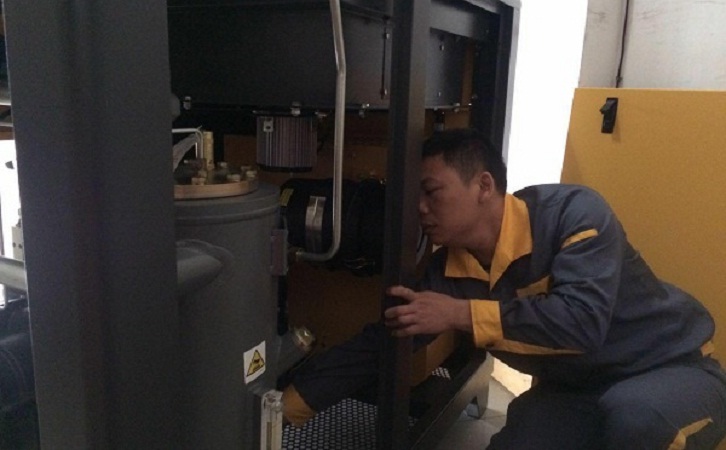
Operator Responsibilities
As a critical piece of equipment, screw air compressors require careful attention. Operators are responsible for:
- Ensuring the compressor and its components are well-maintained.
- Familiarizing themselves with the compressor’s structure, operation, and safety protocols.
- Conducting routine checks, monitoring the system for abnormalities, and making adjustments as needed.
- Understanding common faults and troubleshooting procedures to resolve issues promptly.
- Keeping accurate records of machine operation and maintenance.
- Maintaining a clean and safe working environment.
- Ensuring the compressor operates efficiently, reducing energy consumption while maintaining optimal airflow.
Conclusion
Proper operation, maintenance, and troubleshooting of screw air compressors are essential for maximizing their efficiency and lifespan. By following these guidelines, you can ensure safe and reliable performance, while reducing the risk of unexpected downtime or costly repairs. For more information on air compressors and energy-saving solutions, visit Baldor Air Compressors.