Compressed air, as a commonly used power air source in cement plants, provides effective guarantee for the normal operation of cement production. The compressed air system of a cement plant is mainly composed of an air compressor station and a compressed air pipeline network, generally including an air compressor, a buffer tank, a pre-filter, a dryer, a post-filter, a gas storage tank, gas transmission pipelines, and gas consumption points.
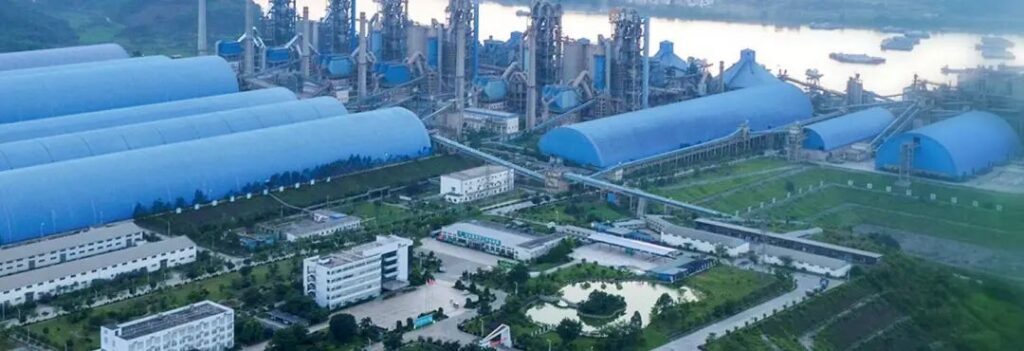
Why does the cement industry need to upgrade the energy efficiency of air compressors?
The air compressor is one of the equipment with relatively large power consumption in cement enterprises. It has the characteristics of low pressure, long operation time, and a large amount of cooling water consumption. Currently, many air compressor units in the cement industry still use piston compressors or fixed-frequency air compressors. These air compressors keep running continuously, generating high noise, consuming a large amount of electricity, and the quality of the used air is not high.
Therefore, how to effectively save energy and reduce the operation cost of air compressors has become an urgent task for cement enterprises.

The Application Scope of Air Compressors in the Cement Industry:
- It mainly supplies air to equipment such as pneumatic valves, instruments, and cylinders.
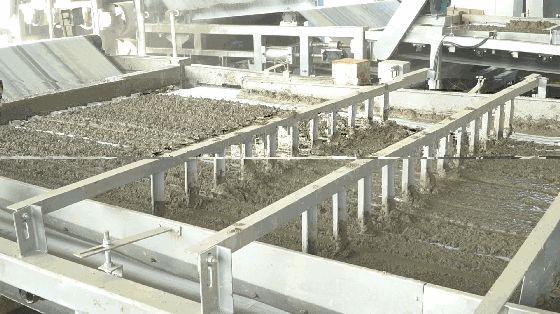
- Cleaning the sealing openings, raw material mixing, dealing with packaging leaks, coal powder, handling the flue dust, clinker cooling, etc.
- In the dry processing procedures, raw materials are transported and mixed through the air compressors used in the cement industry and by means of aeration to form a composition with precise chemical control.
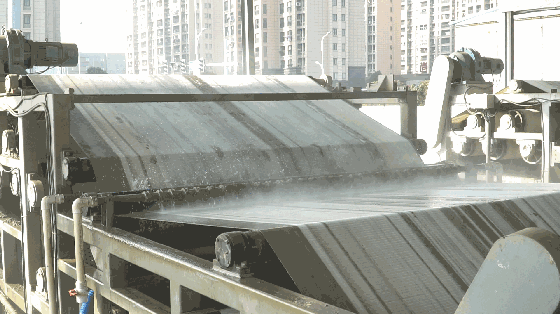
- In the wet processing procedures, air compressors used in the cement industry are applied to mix the slurry, maintain the minerals in the uniform mixture and suspension, and ventilate the warehouses to ensure the free flow and discharge of the powdery materials.
- The largest portion of compressed air in a cement plant is used for transportation.
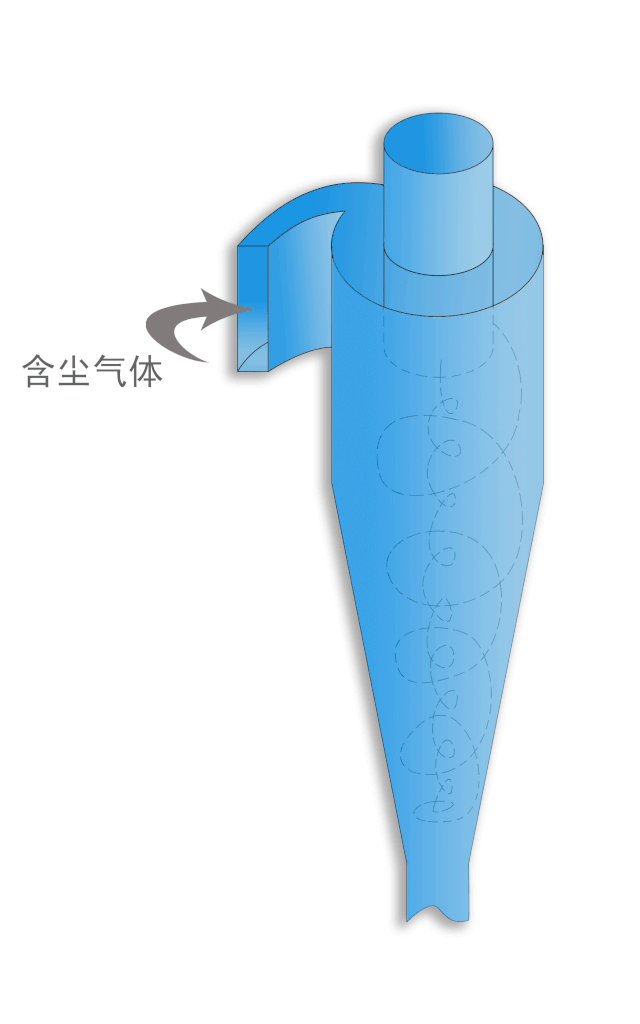
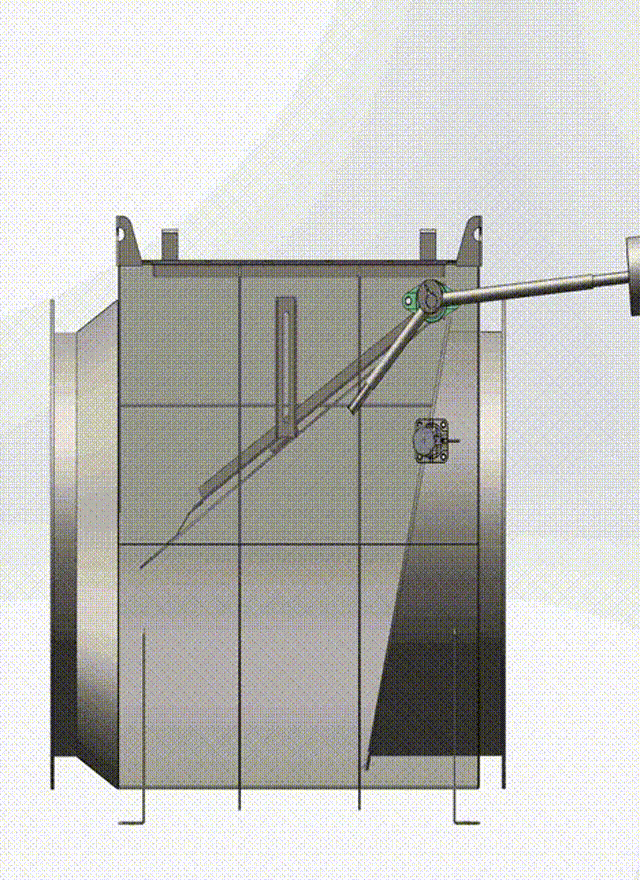
Gas Demand in the Cement Industry:
The total demand for compressed air in the compressed air system of a cement plant is not very large. Therefore, intelligent permanent magnet low-pressure, two-stage compression air compressors are generally selected. For the selection of the dryer, it mainly depends on the local temperature and the user’s demand for the quality of compressed air. When the dew point reaches -70°C, the compressed air can be used as instrument air without damaging the instruments and meters.
Filters are configured to remove impurity particles and oil in the gas. The filtration accuracy reaches 0.01μm, and the oil content of the compressed air at the outlet of the filter is lower than 0.3mg/m³, ensuring the quality of the compressed air. The volume of the gas storage tank can be determined according to the total demand for compressed air.
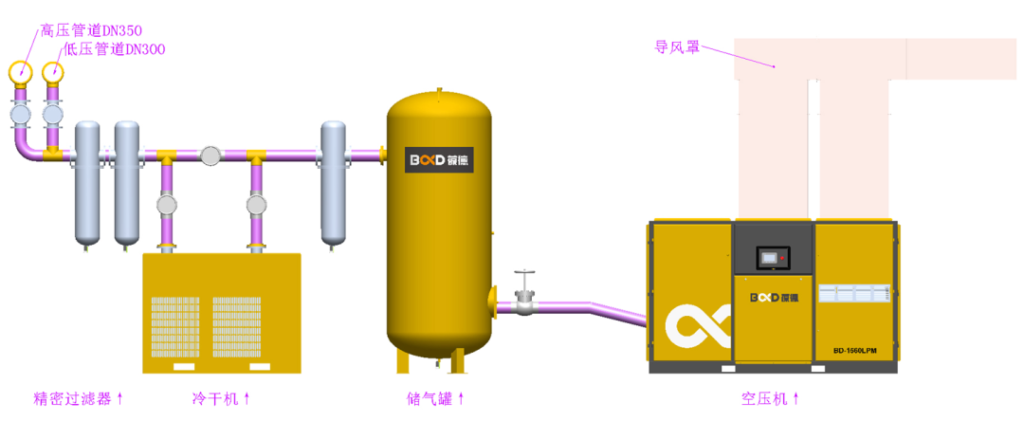
Baldor’s Scientific & Precision-Tailored Gas Solutions
China Resources Cement Holdings Limited (CR Cement), established in 2003, is a Hong Kong-listed company (HKEX: 1313.HK) under China Resources Group, a central state-owned enterprise (SOE). Leveraging its unique resource network and vertically integrated business model spanning cement and ready-mix concrete, CR Cement has established itself as a key player in China’s cement industry under its nationwide unified brand “Runfeng Cement”.
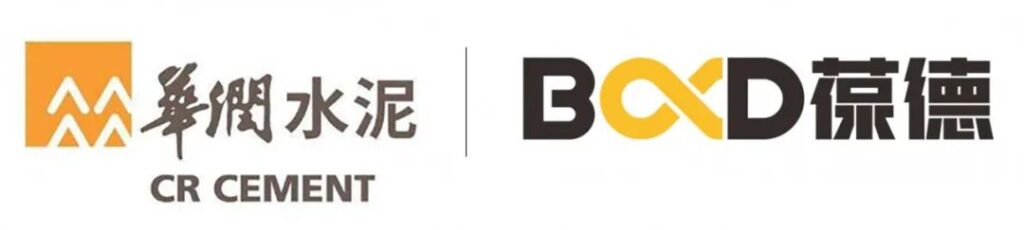
Energy Saving & Emission Reduction, Only by selecting the right air compressor and post-processing equipment, scientifically designing pipeline layouts, and optimizing operational parameters can pressure loss and power consumption be minimized. This enhances production efficiency and reduces costs. With its strong technical expertise and product capabilities, BaldorGroup has become the smart choice for China Resources Cement.
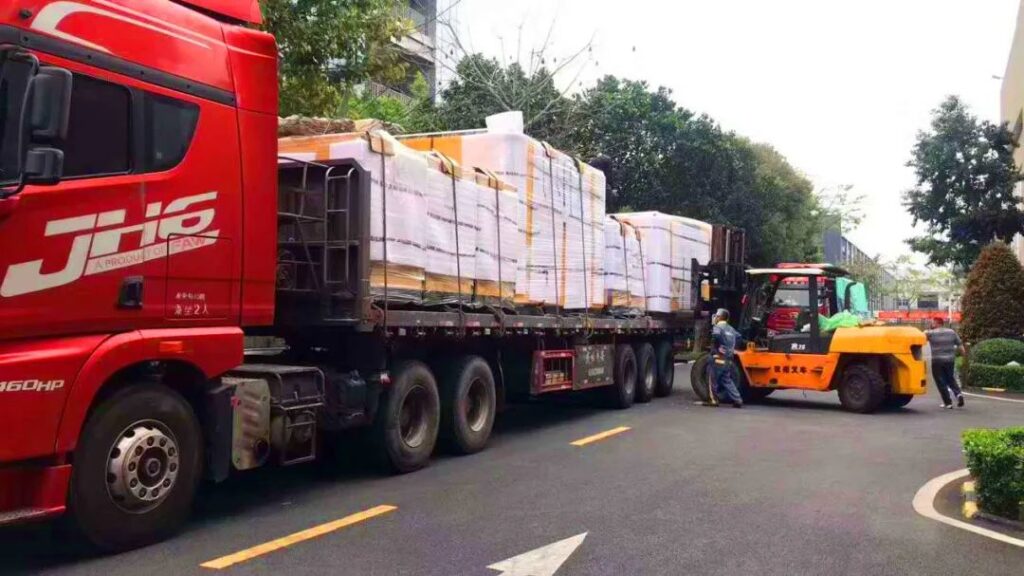
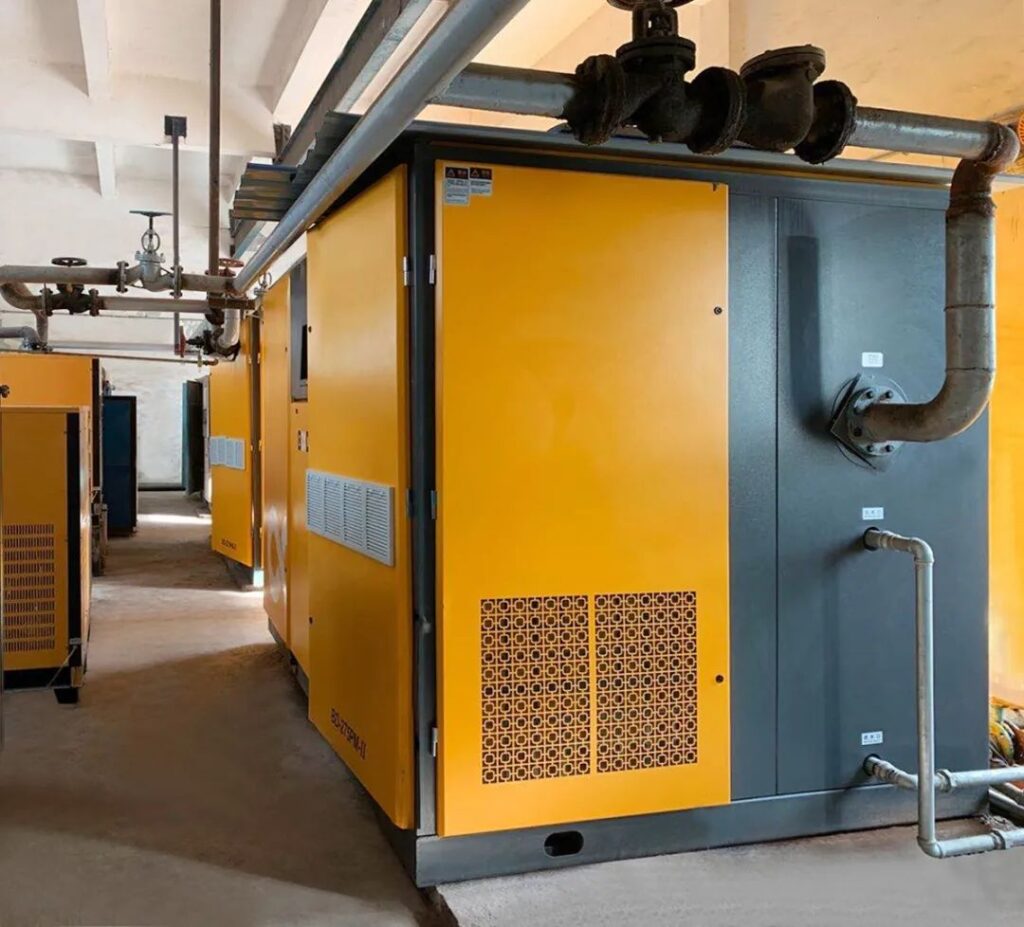
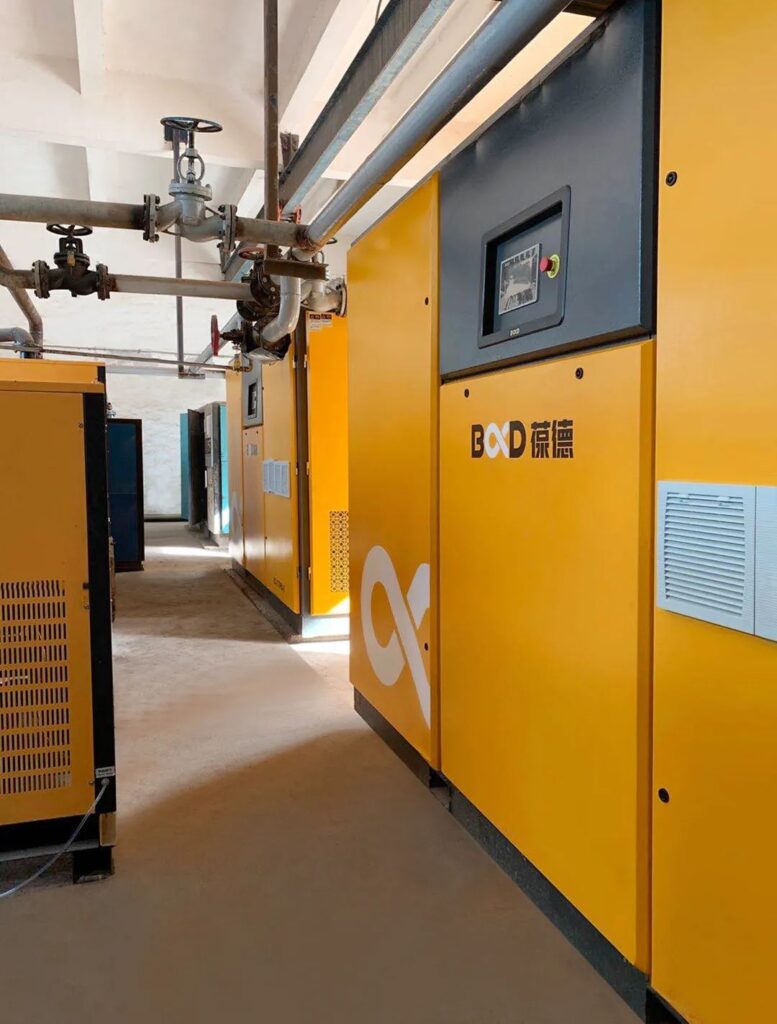
China Resources Group Air Compressor Delivery On-site:
Factors Affecting Air Compressor Energy Consumption,Multiple factors influence the energy consumption of air compressors, including:
Equipment and auxiliary component configurations,Operational management methods,Control system approaches,Only through comprehensive analysis, holistic consideration, and implementation of coordinated measures can energy-efficient, safe, and reliable operation be ensured.The following case studies highlight applications across different cement industry enterprises:
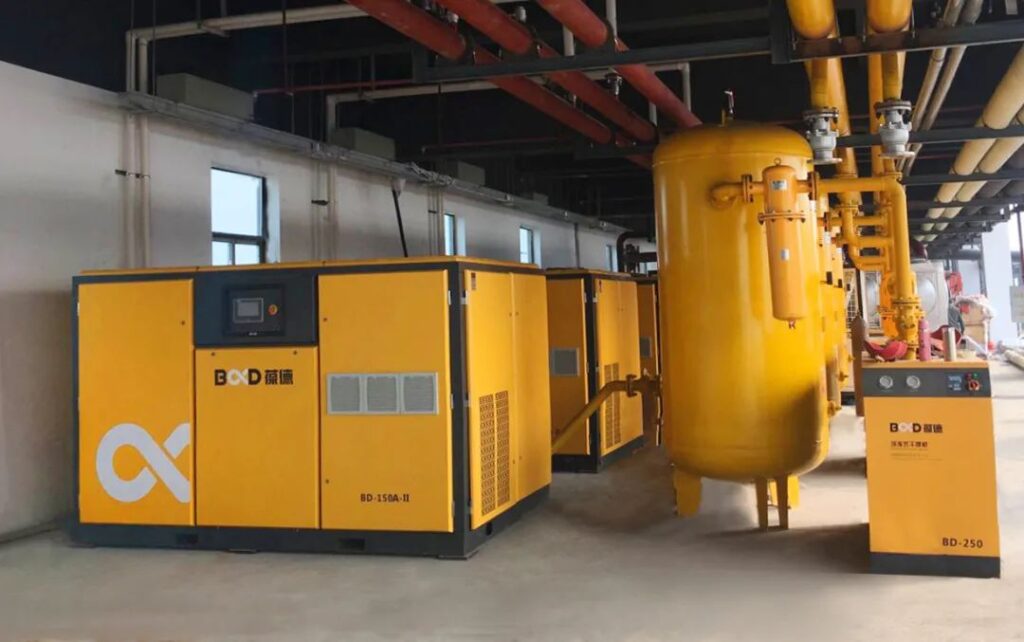
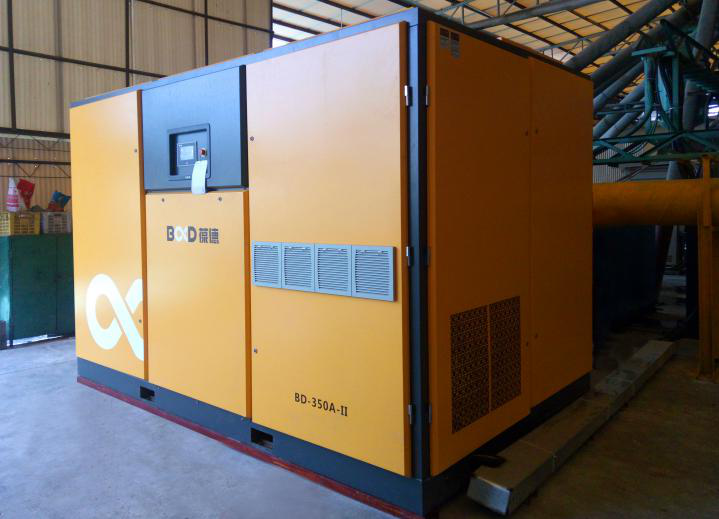
With years of cross-industry experience in customized energy-saving solutions, Baldor provides one-stop, proven system services. Choosing Baldor means choosing reliability!
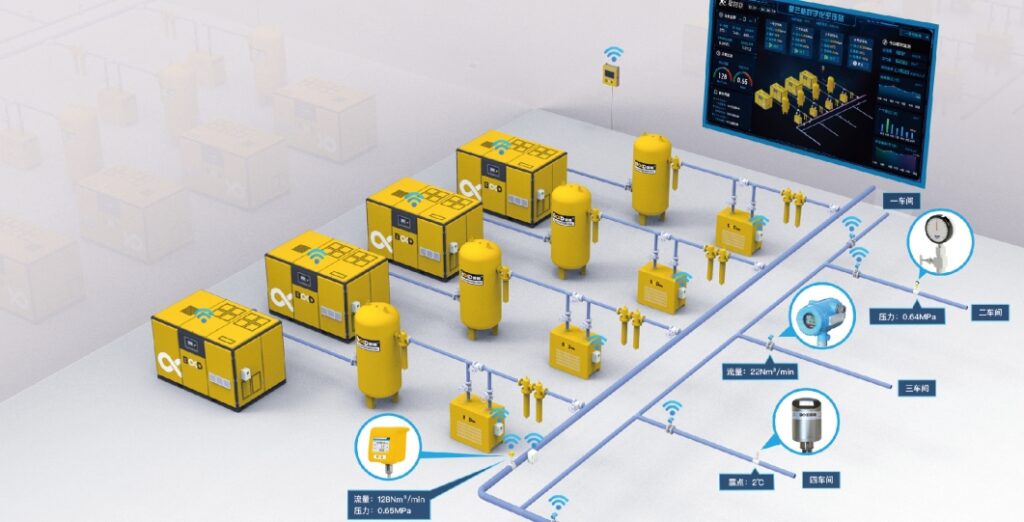